To maintaining machinery and ensuring operational efficiency, vibration testers play a crucial role in predictive maintenance. These devices help identify anomalies in machinery before they lead to significant failures. However, with a myriad of vibration testers available on the market, selecting the right one can be a daunting task. Here are some key factors to consider when choosing a good vibration tester.
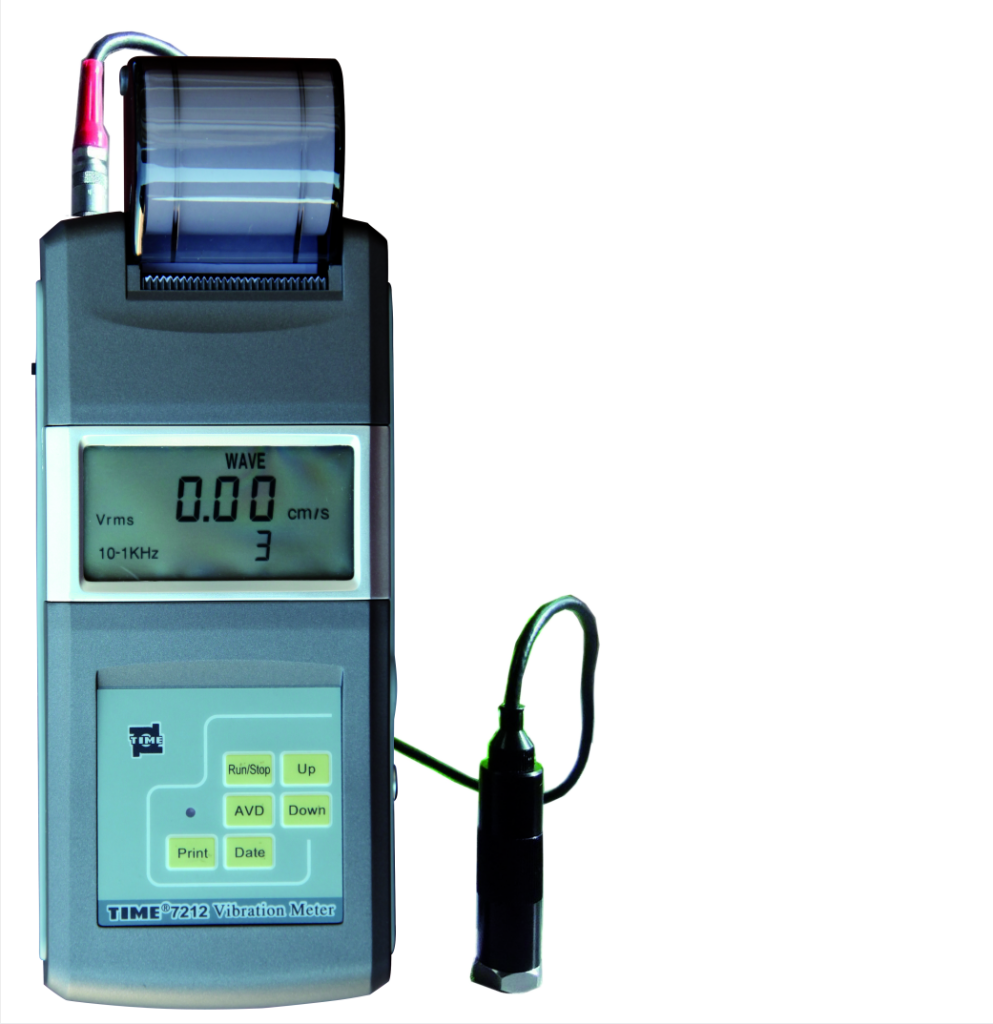
1. Understand Your Needs
Before diving into the specifications and features of different vibration testers, it’s essential to assess your specific needs. Consider the following questions:
– What type of machinery will you be testing? Different machines may have varying vibration profiles.
– What frequency range do you need? Some applications may require high-frequency measurements, while others may only need low-frequency data.
– What level of detail do you require? For basic troubleshooting, a simple handheld device might suffice, whereas more complex machinery may require advanced diagnostic tools.
2. Measurement Capabilities
A good vibration tester should have robust measurement capabilities. Look for the following features:
Frequency Range: Ensure the tester can measure the frequency range relevant to your machinery. Common ranges are from 0.1 Hz to 20 kHz.
Amplitude Measurement: The ability to measure displacement, velocity, and acceleration is crucial for a comprehensive analysis.
Data Logging:If you need to monitor trends over time, choose a tester that can log data for later analysis.
3. Ease of Use
A user-friendly interface is vital, especially for those who may not be highly experienced with vibration analysis. Look for testers that offer:
Intuitive Controls: Simple buttons and a clear display can significantly enhance usability.
Guided Measurements: Some advanced testers provide step-by-step guidance for taking measurements, which can be beneficial for beginners.
Software Integration: If you plan to analyze data on a computer, ensure the device comes with compatible software that is easy to use.
4. Portability and Durability
Consider the environment in which you will be using the vibration tester. A portable and durable device is often preferred for fieldwork. Look for:
Weight and Size: A lightweight and compact design makes it easier to handle and transport.
Build Quality: Ensure the tester is rugged enough to withstand harsh conditions, such as dust, moisture, and temperature extremes.
5. Calibration and Accuracy
Accuracy is paramount when it comes to vibration testing. Check for:
Calibration Standards: Make sure the tester complies with industry standards for calibration.
Accuracy Ratings: Review the specifications to understand the accuracy of measurements across different ranges.
6. Support and Training
Choosing a vibration tester from a reputable manufacturer can offer additional benefits, such as:
Technical Support: Reliable customer service can help you troubleshoot any issues that arise.
Training Resources: Some companies provide training materials or workshops to help you get the most out of your device.
7. Budget Considerations
Finally, consider your budget. While it may be tempting to choose the cheapest option, investing in a quality vibration tester can save you money in the long run by preventing costly machinery failures. Compare features and prices across different models to find a balance between cost and functionality.
Selecting the right vibration tester is crucial for effective machinery maintenance and monitoring. By understanding your needs, evaluating measurement capabilities, considering ease of use, and factoring in portability, durability, calibration, support, and budget, you can make an informed decision. A good vibration tester not only helps in identifying potential issues but also contributes to the longevity and efficiency of your machinery.