The ultrasonic hardness tester is an advanced instrument that measures the hardness of materials using ultrasonic waves. Unlike traditional hardness testing methods, which may require surface preparation and can be destructive, ultrasonic hardness testing offers a non-destructive and efficient alternative.
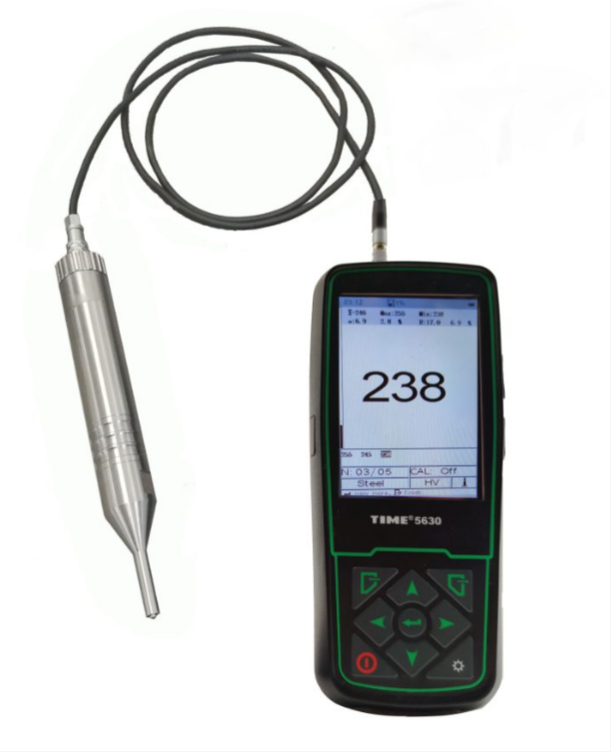
1. Metal Industry
In the metal industry, ultrasonic hardness testers are widely used to assess the hardness of various alloys and metals. These testers provide quick and accurate measurements, which are crucial for quality control during manufacturing processes. By determining the hardness of materials, manufacturers can ensure that their products meet specific standards and specifications. Additionally, ultrasonic testing can identify material inconsistencies and defects that may affect performance.
2. Aerospace Sector
The aerospace sector demands high-performance materials that can withstand extreme conditions. Ultrasonic hardness testers play a vital role in evaluating the hardness of components used in aircraft and spacecraft. By measuring the hardness of critical parts such as turbine blades and structural components, manufacturers can verify that they meet safety and performance requirements. This non-destructive testing method ensures that components can be thoroughly tested without compromising their integrity.
3. Automotive Industry
In the automotive industry, ultrasonic hardness testing is employed to inspect various components, including engine parts, gears, and suspension systems. Ensuring that these components have the appropriate hardness is essential for durability and performance. Ultrasonic hardness testers allow for quick assessments during production, enabling manufacturers to detect any deviations from the desired hardness levels and make necessary adjustments in real time.
4. Tool Manufacturing
Tool manufacturers rely on ultrasonic hardness testers to evaluate the hardness of cutting tools, dies, and molds. The hardness of these tools directly impacts their performance and longevity. By using ultrasonic testing, manufacturers can optimize the heat treatment processes and ensure that their tools maintain the required hardness throughout their lifespan. This not only enhances tool efficiency but also reduces production costs by minimizing tool failure.
5. Research and Development
In research and development settings, ultrasonic hardness testers are invaluable for material scientists and engineers. They facilitate the exploration of new materials and the development of advanced alloys with tailored properties. By providing precise hardness measurements, these testers enable researchers to correlate hardness with other material properties, such as wear resistance and toughness, leading to the innovation of high-performance materials.
6. Non-Destructive Testing
One of the significant advantages of ultrasonic hardness testing is its non-destructive nature. This makes it an ideal choice for evaluating the hardness of components in service, such as pipelines, pressure vessels, and structural supports. Regular hardness testing can help predict the remaining service life of components and prevent catastrophic failures in critical applications.
The applications of ultrasonic hardness testers are vast and varied, spanning across multiple industries. Their ability to provide accurate, non-destructive hardness measurements makes them an essential tool for quality control, research, and development. As technology continues to advance, the use of ultrasonic hardness testers is expected to grow, further enhancing material testing and evaluation processes. By ensuring that materials meet the necessary hardness criteria, industries can improve performance, safety, and reliability in their products.