With the continuous emergence of new technologies and the continuous updating of testing equipment, ultrasonic testing technology, as one of the five major testing technologies in non-destructive testing, occupies an important position in non-destructive testing.

In the inspection process, in addition to the ultrasonic flaw detection instrument, the probe that emits and receives ultrasonic waves also plays an important role. Therefore, the performance of the probe and the appropriate selection of the probe during the flaw detection process will directly affect the accuracy of the flaw detection results. . The following focuses on the classification, functions and selection principles of piezoelectric ultrasonic probes.
- Classification of ultrasonic flaw detector probes
When detecting flaw with ultrasonic flaw detector, different forms of ultrasonic probes need to be used due to the different shape, material, size, surface condition, flaw detection purpose and flaw detection conditions of the workpiece to be tested. Ultrasonic probes can be classified differently according to different induction methods, generally including the following.
1) Classification by wave type: According to the wave type generated in the measured workpiece, it can be divided into longitudinal wave probe, transverse wave probe, plate wave (Lamb wave) probe, climbing wave probe and surface wave probe.
2) Classification by coupling method: According to the coupling method between the probe and the surface of the workpiece to be measured, it can be divided into direct contact probes and liquid immersion probes.
3) Classification according to the direction of the incident sound beam: According to the direction of the incident sound beam, it can be divided into straight probes and oblique probes.
4) Classification by number of elements: According to the number of piezoelectric elements in the probe, it can be divided into single crystal probes, dual crystal probes and polycrystalline probes.
5) Classification by chip material: According to the material of the piezoelectric chip in the probe, it can be divided into ordinary piezoelectric chip probes and composite piezoelectric chip probes.
6) Classification by sound beam shape: According to whether the ultrasonic sound beam is concentrated or not, it can be divided into focused probes and non-focused probes.
7) Classification by spectrum: According to the ultrasonic spectrum, it can be divided into broad-band and narrow-band probes.
8) Classification according to the curvature of the workpiece to be measured: According to the curvature of the workpiece to be measured, it can be divided into flat probes and curved surface probes.
9) Special probes: In addition to general probes, there are also some probes used under special conditions and for special purposes. Such as mechanical scanning switching probe, electronic scanning array probe, high temperature probe, variable angle probe (adjustable from 0° to 90°), porcelain bottle flaw detection flat probe (longitudinal wave) and S-type probe (transverse wave), etc.
- Common functions of typical ultrasonic probes
1) Longitudinal wave probe: Longitudinal wave probe is usually called a straight probe and is mainly used to detect defects parallel to the detection surface, such as forgings, castings, bars, plates, shafts (such as pores, blisters, inclusions, folding and other defects) detection, etc. .
2) Shear wave oblique probe: The shear wave oblique probe uses shear wave detection. It is a probe whose incident angle is between the first critical angle and the second critical angle and the refracted wave is a pure shear wave. It is mainly used for detection perpendicular to or at a certain angle from the detection surface. It is used to detect defects in welds (such as lack of fusion and incomplete penetration), pipes, and forgings (such as cracks, inclusions, etc.).
3) Longitudinal wave oblique probe: The longitudinal wave oblique probe is a probe whose incident angle is smaller than the first critical angle. The purpose is to use small-angle longitudinal waves for defect inspection, or when the attenuation of shear waves is too large, use the characteristics of strong penetration ability of longitudinal waves to conduct oblique incidence inspection of longitudinal waves. When using, attention should be paid to the interference of shear waves in the specimen at the same time.
4) Climbing wave probe: Climbing wave probe is a transducer that uses climbing wave detection. Since the angle of a climbing wave probe is between 75º and 83º, which is almost perpendicular to the thickness direction of the workpiece to be measured, and is close to 90º to the vertical cracks in the workpiece, it has good detection sensitivity for vertical cracks. It is not sensitive to surface roughness, has fast speed, large energy, and long wavelength. The detection depth is deeper than the surface wave. The surface finish requirements of the workpiece are looser than the surface roughness. It is suitable for surface and near-surface crack detection. The main energy used in ultrasonic testing is longitudinal waves.
5) Surface wave probe: The surface wave (Rayleigh wave) probe is a special case of the oblique probe. When the incident angle increases to a certain angle, so that the refraction angle of the transverse wave in the workpiece is 90°, surface waves can be produced in the workpiece. When the straight probe is incident on the workpiece obliquely in the liquid, it can also generate surface waves. Since the energy of surface waves is concentrated within 2 wavelengths below the surface, the sensitivity of inspecting surface cracks is high. It is mainly used to inspect surface or near-surface defects, such as thin plate flaw detection, thin-walled tubes, thin-walled containers, and detection of small near-surface defects. wait.
6) Dual element probe: A dual element probe contains two independent elements in one probe, also known as split probe or combined dual probe. Two piezoelectric chips are installed in a probe holder. One chip emits ultrasonic signals and the other receives them. You can design a specific chip to transmit, or you can design it to transmit to any chip.
Dual-element probes are divided into longitudinal-wave dual-element straight probes and transverse-wave dual-element oblique probes according to the incident angle αL. The dual element probe has the following advantages: high sensitivity, less clutter and small blind area, small length of near-field area in the workpiece, and adjustable detection range. The design of a dual-element probe that emits on one side and receives on the other is particularly suitable for detecting defects very close to the sensor position. Since both the transmitting and receiving parts of the dual-element probe are equipped with delay blocks, this design greatly eliminates near-surface defects. The blind area is very beneficial to the detection of surface defects. Dual element probes have very important applications in ultra-thin parts flaw detection and ultrasonic thickness measurement.
- Principles for selecting ultrasonic flaw detector probes
There are many types of ultrasonic probes with different performances. Therefore, according to the shape of the ultrasonic flaw detection object, the attenuation of ultrasonic waves and the technical requirements, rational selection of probes is the basis for ensuring correct flaw detection results. The choice of ultrasonic probe is mainly reflected in: probe type, probe frequency, probe chip size and probe angle, etc.
3.1 Ultrasonic flaw detector probe type
Generally, the form of the probe is selected based on the shape of the workpiece and the location and direction of possible defects, and the ultrasonic beam axis is perpendicular to the defect as much as possible. For details, please refer to the common typical probe functions section above.
3.2 Selection of ultrasonic flaw detector probe frequency
The frequency of ultrasonic flaw detection is between 0.5-15MHz, and the selection range is large. Generally, the following factors should be considered when selecting frequency.
1) Due to the diffraction of ultrasonic waves, the sensitivity of ultrasonic flaw detection is about one-half wavelength. The speed of ultrasonic waves is constant within the same material, so increasing the frequency will shorten the ultrasonic wavelength and increase the sensitivity of flaw detection, which is beneficial to finding smaller defects.
2) High frequency, small pulse width, and high resolution are helpful for distinguishing adjacent defects and improving resolution.
3) From the diffusion formula, it can be seen that if the frequency is high and the ultrasonic wavelength is short, the half-diffusion angle is small, the sound beam directivity is good, and the ultrasonic energy is concentrated, which is beneficial to finding and locating defects, and the quantitative accuracy is high.
4) It can be seen from the formula of the length of the near field area that the frequency is high, the ultrasonic wavelength is short, and the length of the near field area is large, which is detrimental to flaw detection.
5) From the attenuation and absorption formulas, it can be seen that the attenuation of ultrasonic waves increases sharply with the increase of ultrasonic frequency and medium grain size.
From the above analysis, it can be seen that the frequency of the ultrasonic probe has a greater impact on ultrasonic flaw detection. High frequency, high flaw detection sensitivity and resolution, and good beam directivity are beneficial to flaw detection. However, the frequency is high, the near field area is long, and the medium attenuation is large, which is unfavorable for flaw detection. Therefore, when selecting the frequency of the ultrasonic probe, comprehensive considerations should be taken, all factors should be analyzed, and a reasonable selection should be made. Generally speaking, under the premise of flaw detection sensitivity requirements, a probe with a lower frequency should be selected as much as possible; for forgings, rolled parts and welded parts with fine grains, a probe with a higher frequency is generally used, and 2.5-5.0MHz is commonly used. . For workpieces such as castings and austenitic steels with relatively coarse grains, a soft and low-frequency probe should be used, usually 0.5-2.5MHz. Otherwise, if the frequency is too high, the ultrasonic energy will be severely attenuated.
3.3 Selection of ultrasonic flaw detector probe chip size
The shapes of ultrasonic probe chips are generally round and square. The chip size of the probe has a certain impact on the results of ultrasonic flaw detection. The following factors should be mainly considered when selecting
1) Half diffusion angle: According to the diffusion angle formula, as the chip size increases, the half diffusion angle decreases, the beam directivity is good, and the ultrasonic energy is concentrated, which is beneficial to flaw detection.
2) Flaw detection near field area: It can be seen from the near field area length formula that as the chip size increases, the length of the near field area increases, which is detrimental to flaw detection.
3) Large chip size: The radiated ultrasonic energy is strong, the scanning range of the undiffused area of the probe is large, and the ability to detect long-distance defects is enhanced.
When detecting workpieces with a large flaw area, a large chip probe should be used for flaw detection efficiency; when detecting workpieces with a large flaw thickness, a large chip probe should be used in order to find long-distance defects; for small workpieces, in order to locate and quantify defects accurately, a large chip probe should be used. Select a small element probe; for workpieces with uneven surfaces and large curvatures, in order to reduce coupling losses, a small element probe should be selected.
3.4 Selection of ultrasonic flaw detector probe angle
During inspection, the axis of the ultrasonic sound beam should be perpendicular to the defect as much as possible. Therefore, the angle selection should be based on the type and location of defects that may exist in the inspection object and the allowable flaw detection conditions of the workpiece. The law of reflection and refraction and related geometric knowledge should be used to select the appropriate angle. Probe. Taking the K value of the probe in shear wave detection as an example, the refraction angle has a great influence on the detection sensitivity, the direction of the sound beam axis, and the sound path of the primary wave (the distance from the incident point to the bottom reflection point).
For detecting steel workpieces with organic glass angle probes, when β=40° (K=0.84), the sound pressure reciprocating transmittance is high, that is, the detection sensitivity is high. It can be seen from this that when the K value is large, the β value is large, and the sound path of the primary wave is large. Therefore, in actual detection, when the thickness of the workpiece is small, a larger K value should be selected in order to increase the sound path of the primary wave and avoid detection in the near field area. When the thickness of the workpiece is large, a smaller K value should be selected to reduce the attenuation caused by the excessive sound path and facilitate the discovery of defects at greater depths. In weld inspection, it is also necessary to ensure that the main sound beam can scan the entire weld cross section. For single-sided welding roots that are not penetrated, the problem of end-angle reflection must also be considered, and K=0.7~1.5. Because K<0.7 or K>1.5, the end-angle reflectivity is very low, which can easily lead to missed inspections.
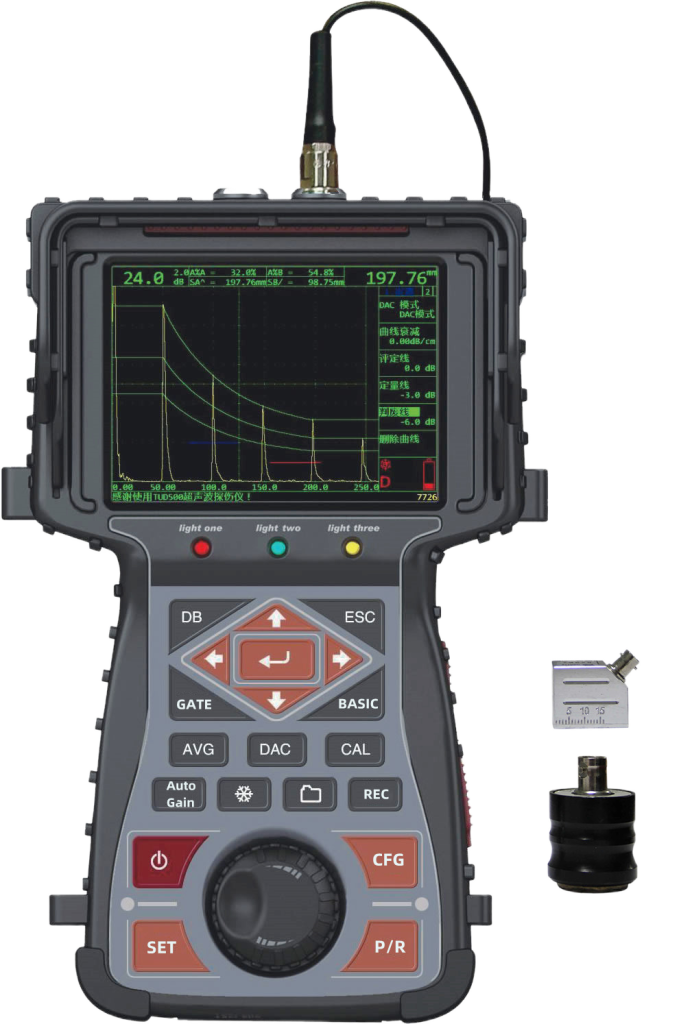