In the ever-evolving world of industrial maintenance and safety, the integrity of gas pipelines is a paramount concern. Gas pipelines, which transport natural gas and other gaseous substances across vast distances, are subject to wear and corrosion over time. To ensure their safety and operational efficiency, regular inspections and monitoring are essential. This is where the TIME2190 high-precision thickness gauge comes into play, offering an advanced solution for detecting and assessing the integrity of gas pipelines.
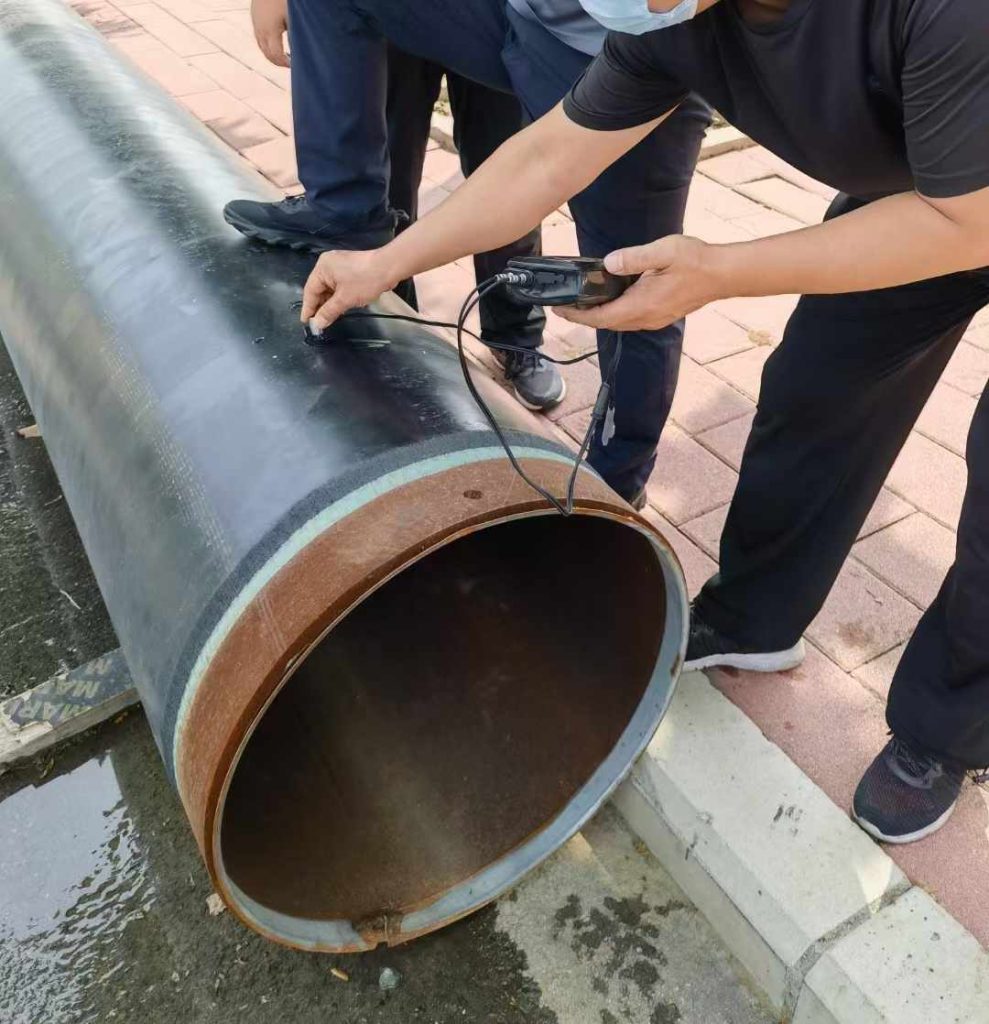
Understanding the Importance of Pipeline Integrity
Gas pipelines operate under high pressure and are often exposed to harsh environmental conditions. Over time, factors such as corrosion, erosion, and mechanical stress can compromise the pipeline’s wall thickness, potentially leading to leaks or catastrophic failures. Regular monitoring of pipeline thickness is crucial for identifying potential issues before they escalate, ensuring the safety of both the infrastructure and the surrounding environment.
The Role of Ultrasonic Thickness Gauges
Ultrasonic thickness gauges, such as the TIME2190, utilize advanced ultrasonic technology to measure the thickness of materials with high precision. By emitting ultrasonic waves and measuring the time it takes for the waves to return after bouncing off the material, these devices can accurately determine wall thickness without causing any damage. This non-destructive testing method is particularly beneficial for gas pipelines, as it allows for continuous monitoring without interrupting operations.
Key Features of the TIME2190 Thickness Gauge
TIME2190 is designed with user-friendly functionality and robust performance in mind. Here are some of its key features:
1. High Precision: The TIME2190 provides accurate thickness measurements within a small margin of error, making it reliable for critical applications in gas pipeline monitoring.
2. Wide Measurement Range: Capable of measuring various materials, including metals and plastics, the TIME2190 is versatile enough to be used across different pipeline types.
3. User-Friendly Interface: The device features an intuitive interface with a clear display, allowing operators to easily navigate through functions and settings.
4. Data Logging Capabilities: The TIME2190 can store measurement data, facilitating trend analysis and historical tracking, which is essential for long-term maintenance planning.
5. Durability and Portability: Built to withstand harsh industrial environments, the TIME2190 is both durable and portable, making it easy to transport to various inspection sites.
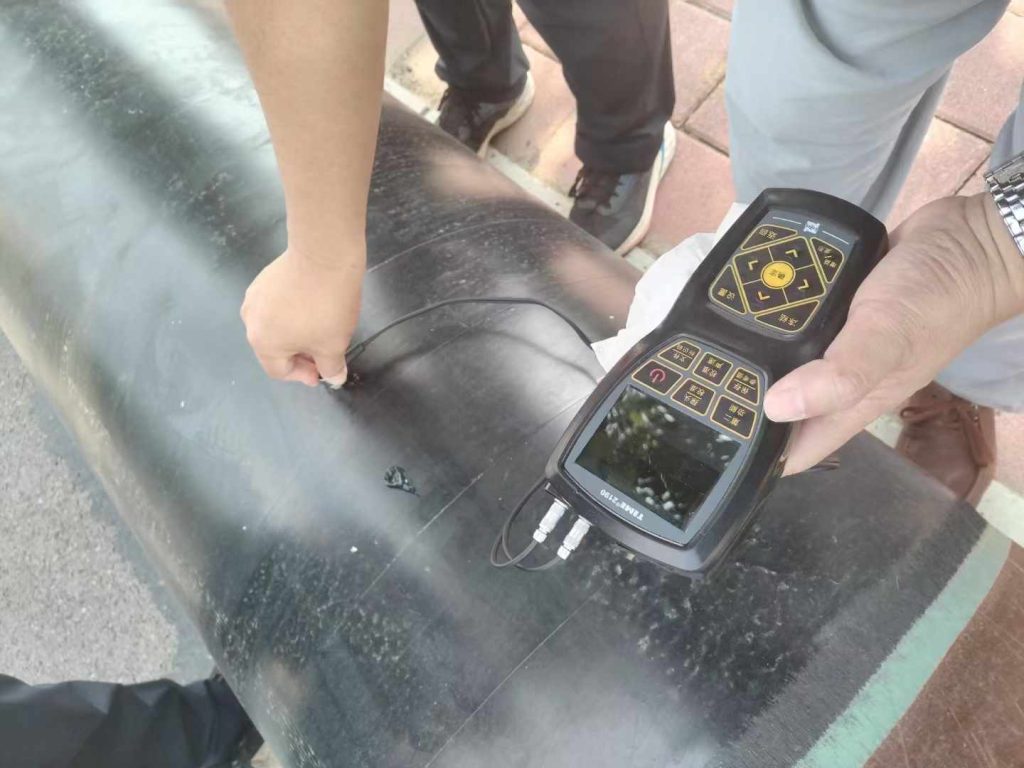
Applications in Gas Pipeline Inspection
TIME2190 is particularly effective in several key areas of gas pipeline inspection:
Routine Maintenance: Regular thickness measurements can help identify areas of concern before they lead to significant problems.
Pre-emptive Assessments: By monitoring wall thickness, operators can make informed decisions about repairs or replacements, ensuring the longevity of the pipeline.
Compliance and Safety: Adhering to regulatory standards is crucial in the gas industry. The TIME2190 aids in demonstrating compliance with safety regulations regarding pipeline integrity.
Emergency Situations: In the event of a suspected leak or failure, rapid assessments with the TIME2190 can provide critical information for emergency response teams.
TIME2190 high-precision thickness gauge represents a significant advancement in the monitoring of gas pipelines. Its ability to deliver accurate, non-destructive measurements makes it an invaluable tool for ensuring the safety and integrity of gas transportation systems. By investing in such technology, operators can enhance their maintenance strategies, comply with safety regulations, and ultimately protect both their assets and the environment. As the industry continues to prioritize safety and efficiency, tools like the TIME2190 will play an increasingly vital role in the future of gas pipeline management.
TIME2190 high-precision thickness gauge can detect gas pipelines and automatically separate the 3PE anti-corrosion layer. It can quickly measure and store large amounts of data, allowing the inspectors to quickly leave the site before conducting report analysis.
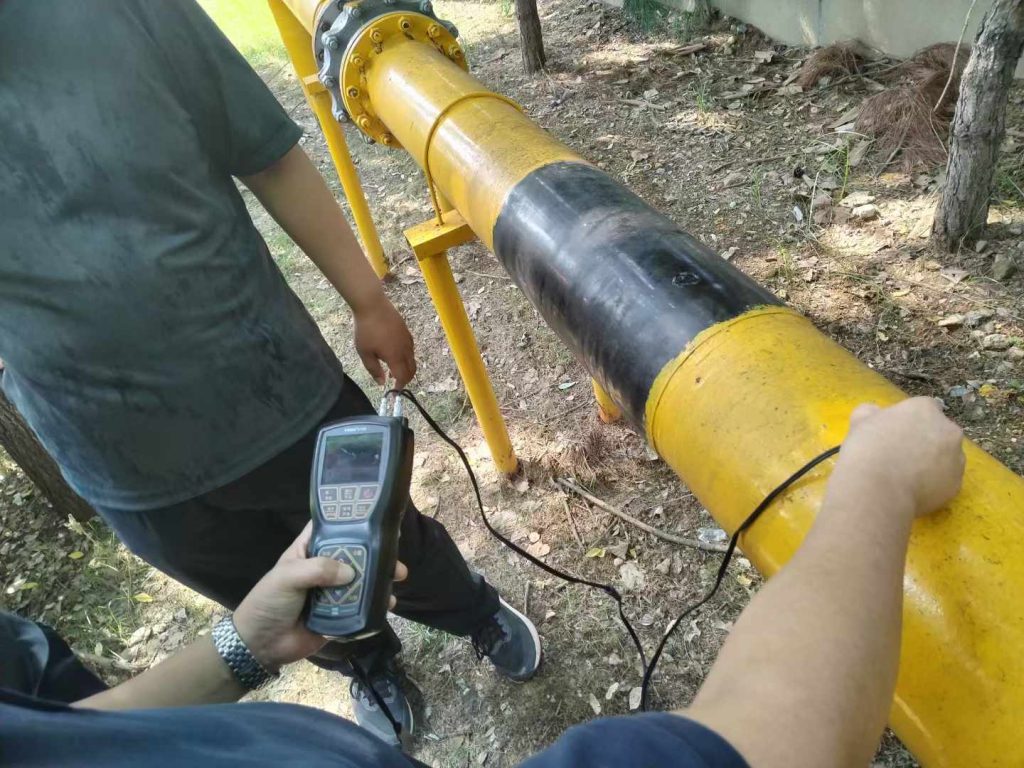