To ensure the integrity and safety of materials and structures, ultrasonic flaw detectors play a crucial role in non-destructive testing (NDT). These devices are used to detect internal flaws, such as cracks, voids, and inclusions in a variety of materials including metals, plastics, and composites.
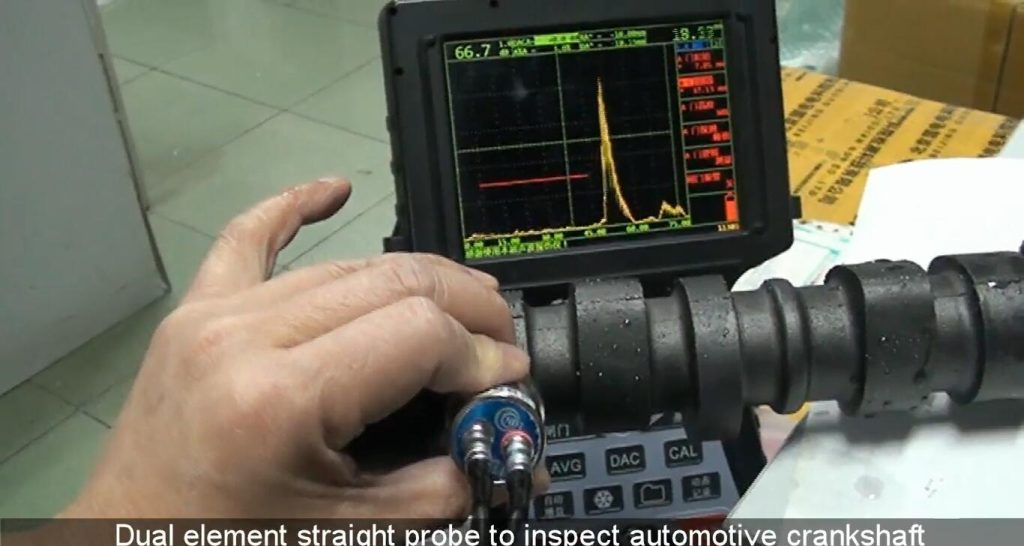
With a myriad of options available on the market, choosing the right ultrasonic flaw detector can be a daunting task. Here are some key considerations to help you make an informed decision.
1. Understand Your Testing Requirements
Before diving into specifications, it’s essential to identify your specific testing needs. Consider the following questions:
– What materials will you be testing? Different materials may require different frequencies and types of transducers.
– What types of flaws are you looking to detect?** The size and nature of the flaws will influence the choice of equipment.
– What is the thickness of the materials? Thicker materials may require higher frequencies for accurate detection.
2. Frequency and Wavelength
Ultrasonic flaw detectors operate on various frequencies, typically ranging from 0.5 MHz to 25 MHz. Higher frequencies provide better resolution for detecting smaller flaws, while lower frequencies are better suited for thicker materials and deeper penetration.
– **Low Frequency (0.5-2 MHz):** Best for thick materials and deeper flaws.
– **Medium Frequency (2-5 MHz):** A balanced choice for general applications.
– **High Frequency (5-25 MHz):** Ideal for thin materials and fine cracks.
3. Type of Transducer
The transducer is a critical component of the ultrasonic flaw detector. There are several types of transducers, each suited for different applications:
– Contact Transducers: These require direct contact with the test surface and are versatile for most applications.
– Immersion Transducers: Used in environments where the test piece can be submerged in water or another coupling medium, providing excellent sensitivity.
– Angle Beam Transducers: Designed for inspecting welds and detecting flaws at specific angles.
Choose a transducer that aligns with your specific testing applications and the materials you will be working with.
4. Display and User Interface
A user-friendly interface can significantly enhance the efficiency of your inspections. Look for detectors with:
– Clear LCD Display: High-resolution screens that are easy to read in various lighting conditions.
– Intuitive Controls: Simple navigation and menu structures allow for quicker operation and training of new users.
– Data Logging and Reporting Features: These functionalities are crucial for documenting test results and facilitating analysis.
5. Portability and Durability
If your testing requires fieldwork, consider the portability of the ultrasonic flaw detector. Look for lightweight models with rugged designs that can withstand harsh environments. Features to consider include:
– Battery Life: Long-lasting batteries are essential for extended testing sessions.
– Water and Dust Resistance: Ensure the device is rated for use in challenging conditions.
6. Calibration and Standards Compliance
Ensure that the ultrasonic flaw detector complies with relevant industry standards and can be easily calibrated. This is crucial for maintaining the accuracy and reliability of your inspections.
7. Budget Considerations
Ultrasonic flaw detectors come in a range of prices, from basic models to advanced systems with extensive features. Determine your budget early on, but remember that investing in a quality device can save you money in the long run by reducing the risk of undetected flaws.
Choosing the right ultrasonic flaw detector requires careful consideration of your specific testing needs, the types of materials involved, and the features that will enhance your inspection process. By taking the time to evaluate these factors, you can select a device that not only meets your requirements but also ensures the safety and integrity of your projects. Whether you are in manufacturing, construction, or maintenance, the right ultrasonic flaw detector is an invaluable tool in your NDT arsenal.