Die Rückprallmethode wird in meinem Land seit mehr als 40 Jahren verwendet, um die Druckfestigkeit von Beton zu testen. Aufgrund seiner Einfachheit, Flexibilität, Genauigkeit, Zuverlässigkeit, Geschwindigkeit und Wirtschaftlichkeit wird es von technischem Prüfpersonal bevorzugt. Es ist die in meinem Land am weitesten verbreitete Methode bei der technischen Inspektion.
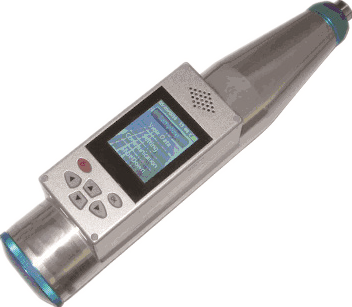
Eines der umfangreichsten Prüfinstrumente. Bei Zweifeln an der Qualität des Ingenieurbauwerks kann zur Prüfung das Rückprallverfahren eingesetzt werden. Bei der Verwendung der Rückprallmethode treten jedoch immer noch viele Probleme wie unregelmäßiger Betrieb, Willkür und ungeeignete Berechnungsmethoden auf, die zu großen Testfehlern führen.
Die Frage, wie die Erkennungsgenauigkeit sichergestellt werden kann, damit sie bei der Überwachung und Inspektion der Bautechnik und der Betonqualität ihre gebührende Rolle spielen kann, ist für viele Projektentwickler zu einem Thema geworden, das ihnen Sorgen bereitet. Um die Erkennungsgenauigkeit der Rebound-Methode zu verbessern, sollten die folgenden Faktoren umfassend berücksichtigt werden.
- Beachten Sie die geltenden Bedingungen für den Rückpralltest
Bei der Rückprallmethode handelt es sich um eine Methode, bei der mithilfe eines Rückprallmessgeräts die Oberflächenhärte von Beton ermittelt und die Festigkeit des Betons berechnet wird. Wenn die Anzahl der standardmäßig aushärtenden Proben nicht ausreicht oder die Proben nicht gemäß den Vorschriften hergestellt werden; es bestehen Zweifel an der Betonfestigkeit des Bauteils; oder die Prüfung der Proben. Bei Zweifeln an den Ergebnissen kann die Prüfung nach den „Technischen Regeln für die Prüfung der Druckfestigkeit von Beton im Rückprallverfahren“ (JGJPT2322001) (im Folgenden „Vorschriften“ genannt) durchgeführt werden. Dabei ist zu beachten, dass Voraussetzung für den Einsatz des Rückprallverfahrens ist, dass die innere und äußere Qualität des zu prüfenden Betons grundsätzlich gleichbleibend ist. Wenn ein erheblicher Unterschied zwischen der Oberflächenschicht und der inneren Qualität des Betons besteht, z. B. wenn er unter chemischer Korrosion, Feuer, Erfrierungen oder inneren Mängeln leidet, kann der Rückprall nicht direkt verwendet werden. Methode zur Prüfung der Festigkeit von Beton. - Vor dem Test muss ein Kalibrierungstest des Rückprallhammers durchgeführt werden. Die Qualität und Prüfleistung des Rückprallhammers wirken sich direkt auf die Genauigkeit der Schätzung der Betonfestigkeit aus. Nur ein Rückprallhammer mit guter Leistung kann die Zuverlässigkeit der Testergebnisse gewährleisten. Im Standardzustand sollte sich der Rückprallhammer auf einem Standardstahlamboss mit einer Rockwellhärte HRC von 60 12 befinden. Nach drei vertikalen Sprüngen nach unten sollte die durchschnittliche Geschwindigkeitseinstellung 80 12 betragen. Andernfalls muss der Schlaghammer eingestellt bzw. kalibriert werden. prüfen. Bei der Prüfung eines einzelnen Bauteils ist es in der Regel lediglich erforderlich, dieses vor der Prüfung zu kalibrieren. Bei groß angelegten Inspektionen nimmt der Rückprall jedoch aufgrund des Einflusses von Faktoren wie Staub vor Ort und der Stabilität des Rückprallhammers selbst mit zunehmender Arbeitszeit ab. Der Arbeitsstatus des Instruments sinkt allmählich unter den Standardstatus. Manchmal gibt es einen großen Unterschied in den Einstellungen der Rückprallhammerrate vor und nach der Prüfung eines Chargenprüfgegenstands, was zu schlechten Testergebnissen führt. Daher sollten bei Tests in großen Mengen Standard-Stahlambosse mitgeführt werden, damit diese jederzeit kalibriert und ausgetauscht werden können, um die Genauigkeit der Testergebnisse sicherzustellen.
- Der Messbereich muss korrekt ausgewählt werden
Bei der Anordnung des Messbereichs zum Testen von Komponenten sollte der Abstand zwischen zwei benachbarten Messbereichen innerhalb von 2 m kontrolliert werden. Der Abstand zwischen der Messfläche und dem Ende des Bauteils bzw. der Kante der Arbeitsfuge sollte nicht größer als 0,5 m und nicht kleiner als 0,2 m sein; Der Messbereich sollte sein. Wählen Sie den Rückprallhammer in horizontaler Richtung aus, um die Betongießfläche zu erfassen, und wählen Sie ihn auf zwei symmetrischen messbaren Flächen aus. Kann diese Anforderung nicht erfüllt werden, kann man es auch auf einer messbaren Fläche wählen, allerdings muss es gleichmäßig verteilt sein. Messbereiche müssen an wichtigen Teilen und Schwachstellen von Bauteilen angeordnet werden, eingebettete Teile sollten vermieden werden. Beim Auftreffen auf kleine dünnwandige Bauteile ist es nicht ratsam, den Messbereich so anzuordnen, dass die Vibrationen, die das dünnwandige Bauteil beim Aufprall erzeugt, zu einem Verlust der Rückprallenergie führen und die Erkennungsergebnisse verschlechtern. Wenn eine Prüfung erforderlich ist, sollte diese zuverlässig abgestützt werden, damit sie vor der Prüfung über eine ausreichende Bindungskraft verfügt. - Testaktionen müssen standardisiert sein und zufällige Vorgänge vermeiden.
Die Rebound-Methode selbst ist eine wissenschaftliche Betriebsmethode, und das Land hat auch speziell entsprechende Vorschriften formuliert, die es den Betreibern nicht erlauben, nach Belieben zu arbeiten. Die Genauigkeit des Rückpralls hängt auch davon ab, ob die Kraft des Bedieners angemessen und gleichmäßig ist, ob sie senkrecht zur Oberfläche der Struktur oder des Bauteils ist und ob der Vorgang standardisiert ist. Bei tatsächlichen Tests führen jedoch nur wenige Personen Testvorgänge in strikter Übereinstimmung mit den in den Standards festgelegten technischen Anforderungen durch. Sie haben ein schwaches Verantwortungsbewusstsein und sind oberflächlich. Solche Tests führen zu großen Testfehlern und können die Rückprallqualität nicht garantieren. Aus diesem Grund sollten wir die Berufsethik des Inspektionspersonals stärken und die Inspektionsverantwortung verbessern. Dies sind die einzigen Möglichkeiten, die Inspektionsgenauigkeit der Rückprallmethode wirklich zu verbessern. - Beseitigen Sie den Einfluss von Testoberflächenfaktoren
Die „Vorschriften“ legen fest, dass die Oberfläche von Betonbauteilen, die für Rückpralltests verwendet werden, sauber und glatt sein muss und keine losen Schichten, Leim, Fett, Waben oder narbige Oberflächen aufweisen darf. Bei der Inspektion stoßen wir häufig auf Bauteile mit narbiger Oberfläche oder Leim. Sie müssen vor dem Zurückfedern mit einer Schleifscheibe geglättet werden, sonst ist das Ergebnis gering. Unter der Voraussetzung, dass die Testoberfläche sauber und eben ist, muss auch darauf geachtet werden, ob die Betonoberfläche trocken ist. Der Feuchtigkeitsgehalt des Betons beeinflusst seine Oberflächenhärte. Nach dem Einweichen des Betons in Wasser nimmt seine Oberflächenhärte ab. Daher hat die Luftfeuchtigkeit auf der Betonoberfläche einen großen Einfluss auf den Rückpralltest. Bei nassem oder wassergetränktem Beton muss die Oberfläche vor der Prüfung getrocknet werden. Es wird empfohlen, die natürliche Trocknungsmethode zu verwenden. Es ist verboten, heißes Feuer oder eine Stromversorgung zur Zwangstrocknung zu verwenden, um zu verhindern, dass die Betonoberfläche verbrennt und die Erkennungsgenauigkeit beeinträchtigt wird. - Achten Sie auf den Testwert der Karbonisierungstiefe.
Die Genauigkeit der Messung des Karbonatisierungstiefenwerts wirkt sich wie der Rückprallwert direkt auf die Genauigkeit der Schätzung der Betonfestigkeit aus. Beachten Sie beim Testen der Karbonisierungstiefe, dass der Tiefenwert der vertikale Abstand und nicht der im Loch vorhandene nicht vertikale Abstand sein sollte. Das Pulver und die Ablagerungen im Loch müssen vor der Messung entfernt werden, andernfalls ist es schwierig, zwischen karbonisierten und nichtkarbonisierten Grenzen zu unterscheiden, was zu großen Testfehlern führt. Bei der Messung des Verkokungstiefenwerts ist es am besten, anstelle einer Sichtprüfung spezielle Messgeräte zu verwenden. Es gibt noch eine weitere Situation, der besondere Aufmerksamkeit gewidmet werden sollte. Bei der Prüfung der Karbonisierungstiefe von mit Stuckmörtel überzogenen Bauteilen ist die Prüfoberfläche durch das Füllen und Eindringen von Zementmörtel beeinträchtigt und weist in der Oberflächenschicht einen hohen Alkaligehalt auf. Die für den Karbonisierungstest verwendete Phenolphthaleinalkohollösung stößt auf Das Alkali wird sofort rot, was leicht zu visuellen Fehlern führen kann, da der Wert der Karbonisierungstiefe sehr gering ist. Wenn Sie das Testloch genau beobachten, können Sie feststellen, dass die Farbe der äußeren Schicht dunkler, die Farbe des Betons im Inneren des Lochs jedoch heller ist. Die Dicke des helleren Farbanteils ist die tatsächliche Karbonisierungstiefe des Betons. Die Inspektoren müssen darauf achten, diesen subtilen Unterschied zu erkennen. - Achten Sie auf die Korrektur des Betonrückprallwerts
In den letzten Jahren, mit der Verbreitung von Pumpbeton in Städten, wird der Temperaturwert des Betons im Messbereich, der mit der Rückprallmethode gemäß der Umrechnungswerttabelle für die Betonfestigkeit geschätzt wird, im Messbereich deutlich niedriger sein als sein tatsächlicher Festigkeitswert . Dies liegt daran, dass der gepumpte Beton eine hohe Fließfähigkeit aufweist, die Partikelgröße der groben Zuschlagstoffe klein ist, der Sandanteil zunimmt, die Mörtelbeschichtungsschicht des Betons dicker ist und die Oberflächenhärte gering ist. Daher ist es bei der Verwendung der Rückprallmethode zur Prüfung der Betonfestigkeit erforderlich, die Methode des Betongießens durch die Baueinheit im Voraus zu verstehen und auf Korrekturen zu achten. Wenn sich das Rückprallmessgerät während des Tests außerdem in einer nicht horizontalen Richtung befindet und die Testoberfläche eine nicht betonierte Seite ist, muss der Rückprallwert zuerst entsprechend dem Rückprallwert während der nicht horizontalen Zustandsprüfung korrigiert werden und dann anders Gießvorgänge müssen entsprechend dem winkelkorrigierten Rückprallwert durchgeführt werden. Der Rückprallwert der Oberfläche sollte korrigiert werden. Die Reihenfolge solcher Korrekturen kann nicht umgekehrt werden, noch können die separat korrigierten Werte direkt zu den ursprünglichen Werten addiert oder von ihnen subtrahiert werden, da dies sonst zu Berechnungsfehlern führt und die Schätzung der Betonfestigkeit beeinträchtigt. - Wenn der Test abnormal ist, muss er in Verbindung mit der Kernbohrmethode verwendet werden. Im aktuellen Ingenieurbau werden häufig große Schalungen mit Sperrholzoberfläche verwendet. Diese Art von Schalung weist eine hervorragende Dichtleistung auf, ist jedoch nicht luftdurchlässig. Die beim Rüttelvorgang entstehenden Blasen sammeln sich an der Betonoberfläche und der Großfläche. Die Entladung zwischen den Schalungen ist schwierig, was dazu führt, dass nach dem Entfernen der Schalung viele kleine Poren auf der Betonoberfläche entstehen, wodurch die Betonoberfläche nicht sehr dicht ist. Wenn die Aushärtung des Betons nicht mithalten kann, ist die Betonoberfläche nicht in der Lage, die Hydratationsreaktion effektiv durchzuführen, und es kommt nicht nur zu einer Pulverisierung. und die Karbonisierungstiefe des Betons ist relativ groß, was zu einer geringen Betonoberflächenfestigkeit führt. Als beispielsweise in einem Gewerbe- und Wohngebäude mit Rahmenkonstruktion in unserer Stadt ein Rückprallmessgerät verwendet wurde, um den Beton der dreistöckigen Wandscheibe stichprobenartig zu prüfen, wurde festgestellt, dass die Oberflächenfestigkeit des Betons aller beprobten Komponenten war relativ niedrig und erreichte nur 67 % des ursprünglich vorgesehenen Festigkeitsniveaus. Nach Überprüfung der bautechnischen Daten wurde festgestellt, dass es keine Probleme mit dem Betonmischungsverhältnis und den im Projekt verwendeten Rohstoffen gab. Auch die Verwaltung des Betons nach dem Mischen durch die Baueinheit war vorhanden. Daher wurde die Kernbohrmethode zur Entnahme von Proben zur erneuten Untersuchung eingesetzt. Die Kernprobe wurde untersucht und die Oberflächenschicht des Betons betrug 10 mm. Lose. Die Innenschicht ist relativ hart und das Testergebnis der Kernprobe zeigt, dass die tatsächliche Druckfestigkeit des Betons mit der ursprünglichen Entwurfsfestigkeit übereinstimmt, wodurch Fehleinschätzungen vermieden werden.
- Erstellen Sie eine spezielle Kraftmesskurve für diese Region
Obwohl die nationale Norm eine Festigkeitsmesskurve für den nationalen universellen Rückpralltest und eine Umrechnungstabelle für Betonfestigkeitswerte bereitstellt, berücksichtigt die nationale einheitliche Kurve nur die Verwendung von Rohstoffen im ganzen Land und unterscheidet nicht zwischen gebrochenem und gekieseltem Normalbeton . Tatsächlich gibt es jedoch einen großen Unterschied in der Festigkeit von gebrochenem und kiesigem Normalbeton, der mit der Rückprallmethode getestet wurde. Die regionale Festigkeitsmesskurve ist eine Kurve, die durch Tests, Verifizierung und Korrektur unter vollständiger Berücksichtigung der Betonrohstoffe, der klimatischen Bedingungen sowie der Nährstoff- und Erhaltungsprozesse in der Region erstellt wurde. Im Vergleich zur universellen Kraftmesskurve ist diese Kurve besser als die universelle Kraftmesskurve. Es liegt näher an den experimentellen Daten und kann die tatsächliche Festigkeit von Beton in der Region besser abschätzen. Daher kann die Erstellung einer speziellen Kraftmesskurve für diesen Bereich die Erkennungsgenauigkeit der Rückprallmethode effektiv verbessern.